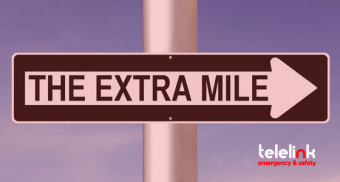
In this short article, we’re going to share 3 safety practices that you won’t find in your OSHA standards handbook but are probably a good idea to do anyway. We hope that by sharing these best practices, you can elevate your safety program to go above and beyond OSHA & OHS minimum requirements.
-
Transformer safety for linesmen:
Contribution from: Yard Superintendent with 30 years of experience
Industry: Hydro utilities
Their practice: Transformer marking
Working on transformers poses a non-technical challenge; they all look the same. In addition to normal lockout procedures, this Hydro company will mark transformers that are being worked on with a visual marker – like a small coloured piece of tape. Now, if a contractor or yard attendant enters the yard after regular hours, the piece of equipment that is already locked out is clearly identified to them as well. This simple practice ensures that nobody accidentally contacts a live transformer, and equipment identification is easier in general.
Honourable mention: Any vehicle or piece of equipment that has to travel through the yard must move clockwise. This can help reduce the chaotic nature of the yard and provide a degree of predictability to the people working and driving. -
Working in remote or isolated areas
Contribution from: Branch Manager with 18 years of experience
Industry: Telecommunications
Their practice: The buddy system
This company does almost everything in pairs of two, regardless of whether the task is a one or two-person job. When asked about the reasoning behind such a cost-intensive practice, we were told “First of all, we don’t want to see anyone get hurt, and secondly, while it may be more of an upfront expense, it is cheaper than having a significant injury, or having an employee miss a significant period of time.”
Yes, but: Working in pairs all the time is very expensive. A cost-effective alternative to working in pairs is to leverage lone worker apps or devices with a 24/7 monitoring team. A lone worker app enables employees working alone to safely check-in with a monitoring team at scheduled intervals. If the employees fail to check-in, the monitoring team can message the employee to ensure they are okay, or dispatch emergency help when needed. These apps often have features such as exact location, panic button, and even no motion detection. -
Evolving safety education
Contribution from: OHS Manager with 4 years of experience
Industry: HVAC
Their practice: Extra training
This company places an emphasis on additional training and learning. The focus on continued safety education helps the entire team stay sharp and never become complacent. For example, the entire team working at the HVAC company are trained in first aid, when most locations (depending on what country, state, or province you live in) only require one person on site to be trained in first aid at any given time.
In addition to team-wide first aid initiatives, they also encourage OHS managers to broaden their safety education with courses in adjacent fields. Infection control, inventory management, and even project management.
Creating a culture of safety and compliance
If you wish to create a culture where safety is more than a box to check, you’ll almost certainly have to go above and beyond the minimum requirements as set out by OSHA and OHS authorities. We hope this article encourages you to seek best practices from your peers, never stop learning, and always push for better and safer workplaces.
[Related: 5 ways to create a culture of safety and compliance]
About Telelink
Telelink specializes in complex lone worker solutions and can offer our expertise and experience in crafting yours. Telelink provides 24/7 monitoring and helps you source the best apps, devices or wearable technology to monitor your lone workers. Our dedicated safety team is trained to handle emergency situations with extreme precision. With 911 response times, Telelink’s 24/7 team of safety monitoring professionals are ready to respond to your lone workers the second they need help.
Post a Comment