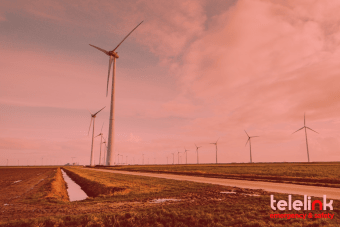
Lone Worker Safety in the Wind Industry
Across North America, employers have a responsibility to keep their employees safe. This poses an extra challenge when employees work without direct supervision or work while alone. In the wind industry this issue is again further complicated by the remote nature of the work performed, and the additional risks that come with performing work at height or around electrical equipment. Additional processes and procedures limit the risk caused by deploying lone workers to the company and to the individual employee, and site-specific plans for dealing with work performed in remote or isolated areas are now a requirement under the ANSI/ASSE A10.21 standard.
Creating a Comprehensive Work Alone Plan
The first step to creating a comprehensive lone worker safety process is to identify who your lone workers are, and where they will be working. A lone worker is any employee who works outside of sight and sound of their co-workers. This means that if an employee is conducting work out of earshot and outside a line of sight, then he or she is also considered a lone worker, even if they have a buddy or teammate assigned to them. It is also important to note that employees who are isolated for only a part of their shift are also considered lone workers.
Once you have identified the lone workers on your team, it is important to assess the environment where they will be working. If they are working alone in an office environment, it is likely relatively low risk, and a check-in solution should suffice. If they are working in an industrial setting such as a wind farm, then additional risks are introduced due to the nature of their particular situation, such as the risks of working with heavy machinery, working at heights, working with electrical equipment, and working in remote areas, including areas without cellular reception.
Assess the Environment and Risk
When dealing with lone working in a high-risk environment, a check-in only solution is not ideal. Check-in only solutions provide a set time interval in which an employee must make contact with someone to confirm that they are okay. The problem with these solutions in a high-risk environment is the chance of something serious occurring during the time interval when no one is looking for that particular employee. This introduces the chance of a highly delayed response to an incident, depending on the amount of time left on the check-in timer when the event occurs. This is not to devalue the power of check-ins, but for higher risk environments, they should be used as a single part of a complete solution for lone workers. [Read more on appropriate check-in intervals here]
Lone Worker Devices and Technology
A complete lone worker solution should include fall detection and no motion monitoring, SOS capabilities, satellite functionality if needed, and check-in timers. These additional capabilities allow workers to feel secure that should an incident occur in between safety check-ins, someone will be made aware of the situation immediately and can dispatch an appropriate response. This is especially valuable for work done in remote locations, where there is already a high chance of long lead times for emergency services.
All employers are responsible for ensuring their employees have the tools and resources necessary to stay safe while working. Now is the time to review your lone worker policies and procedures and ensure that you have the right supports in place to reduce your risk and the risk of your lone workers.
Post a Comment